Ремонт регулирующих и отсечных клапанов выполняется только после их демонтажа с технологического трубопровода. Допускается мелкий ремонт клапана по месту, это:
— Набивка сальникового уплотнения;
— Снятие крышек клапана для проверки внутренних элементов регулирующего органа.
Оформление наряда — допуска на производство ремонтных, газоопасных работ, отключение регулирующих клапанов запорной арматурой, сброс остаточного давления на отключенном участке трубопровода, а также подготовка (промывка, пропарка) клапана к ремонту выполняется технологическим персоналом. Демонтаж и монтаж клапана в ремонт выполняет служба главного механика.
Запрещается ослаблять или подтягивать гайку сальникового уплотнения на не отключённом запорной арматурой регулирующем клапане.
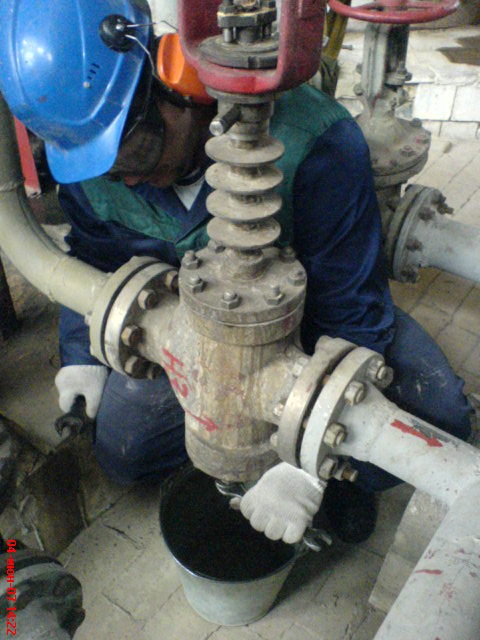
Проведение погрузочно — разгрузочных работ согласно требованиям правил промышленной безопасности и охраны труда.
Погрузочно — разгрузочные работы должны производиться под руководством мастера или специально назначенного ответственного опытного рабочего.
Перед началом работы необходимо:
— надеть спецодежду, спец.обувь и другие СИЗ;
— осмотреть место работы, освещение и т.д.;
— о замеченных опасностях доложить мастеру или ответственному.
На рабочем месте не должны находиться люди имеющие ограничения в перемещении тяжестей. Предельно допустимая масса груза при чередовании подъема и перемещения с другой работой не должна превышать:
— для женщин -10 кг;
— для мужчин — 50 кг.
При перемещении тяжестей более 50 кг работа должна производится механизированным способом (лебедка, тельфер, кран-балка, погрузчик, кран — манипулятор, подъемник (вышка)). К выполнению операций по строповке (обвязке, зацепке, закреплению, подвешиванию на крюк машины, установке в проектное положение и отцепке) грузов в процессе производства работ грузоподъемными машинами допускаются специально обученные квалифицированные рабочие — стропалыцики, имеющие удостоверение на право проведения данных работ.
Неполадки пневматических исполнительных устройств с пружинным мембранным исполнительным механизмом.
1. При плавном изменении давления сжатого воздуха в мембранной полости исполнительного механизма шток и затвор односедельного или двухседельного регулирующего органа перемещается рывками.
Возможные причины |
Способы устранения неполадок |
Торможение штока в сальниковом устройстве регулирующего органа вследствие отсутствия смазки или недопустимо большой затяжки сальника |
Подать смазку в сальниковое устройство с помощью лубрикатора, а если это не приведет к нужным результатам, то осторожно ослабить затяжку сальниковой гайки, наблюдая за тем, чтобы через сальник наружу не стало проникать протекающее вещество |
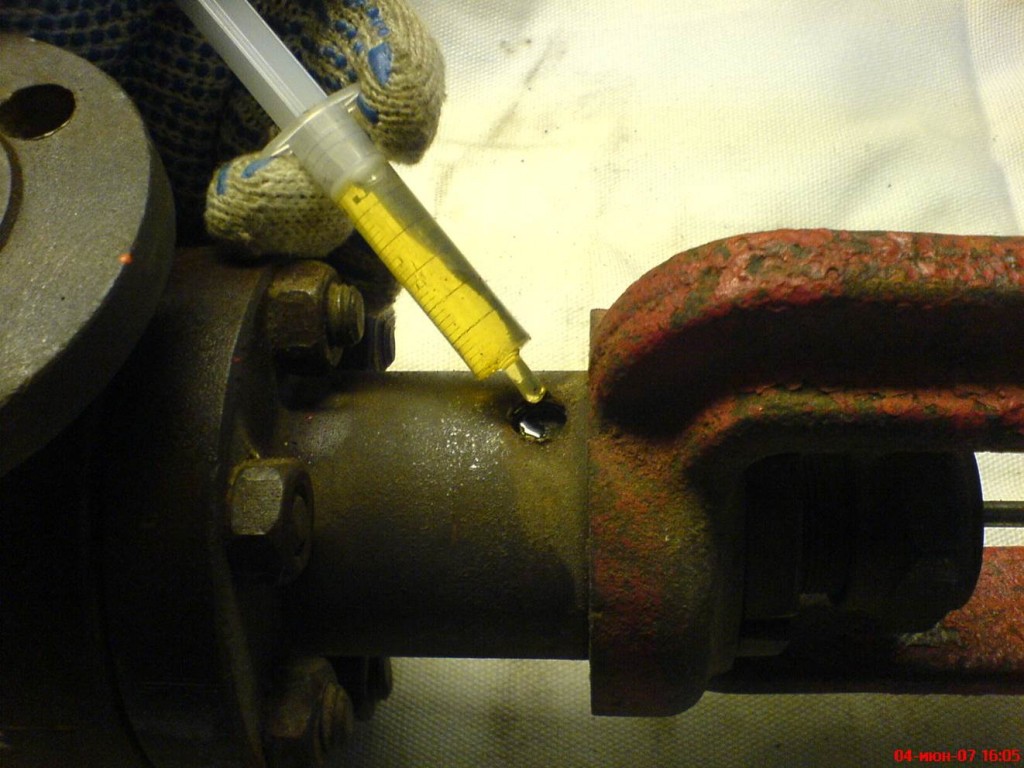
2.Через сальниковое устройство проникает протекающее вещество (жидкость, пар, газ).
Возможные причины |
Способы устранения неполадок |
Недостаточно смазки, слабая затяжка сальника, плохое качество сальниковой набивки |
Добавить смазку, подтянуть сальниковую гайку, сменить сальниковую гайку, сменить сальниковую набивку |
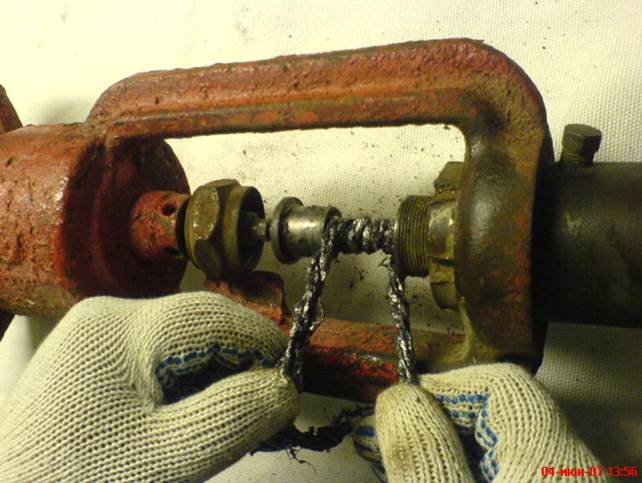
3. При изменении давления сжатого воздуха в мембранной полости исполнительного механизма от минимального до максимального значения шток и затвор односедельного или двухседельного регулирующего органа не перемещаются полностью из одного крайнего положения в другое.
Возможные причины |
Способы устранения неполадок |
Пружина мембранного исполнительного механизма при настройке была сжата больше, чем следует, и поэтому для преодоления усилий, развиваемых ею, требуется увеличенное давление воздуха по сравнению с необходимым при стандартном натяжении пружины |
Постепенно ослабить натяжение пружины до величины, обеспечивающей перемещение штока и затвора из одного крайнего положения в другое при изменении давления воздуха в мембранной полости исполнительного механизма от минимального до максимального нормированных значений |
Пружина мембранного исполнительного механизма недостаточно сжата при настройке и не может преодолеть сил трения, возникающих в подвижной части исполнительного устройства, а также массы этой части и сил от давления протекающего вещества на затвор (поэтому затвор полностью не поднимается) |
Постепенно увеличить натяжение пружины до величины, обеспечивающей перемещение затвора из одного крайнего положения в другое при изменении давления воздуха в мембранной полости от минимального до максимального нормированных значений |
Затвор при своем ходе упирается в посторонний предмет, попавший в мембранное исполнительное устройство (кокс, песок, металлическая прокладка, гайка и т. п.) |
Отключить линию сжатого воздуха от мембранной полости исполнительного устройства, переключив поток на обводную линию, и принять меры к очистке корпуса мембранного исполнительного устройства от посторонних предметов. Убедиться, что поверхности затвора и седел не повреждены
|
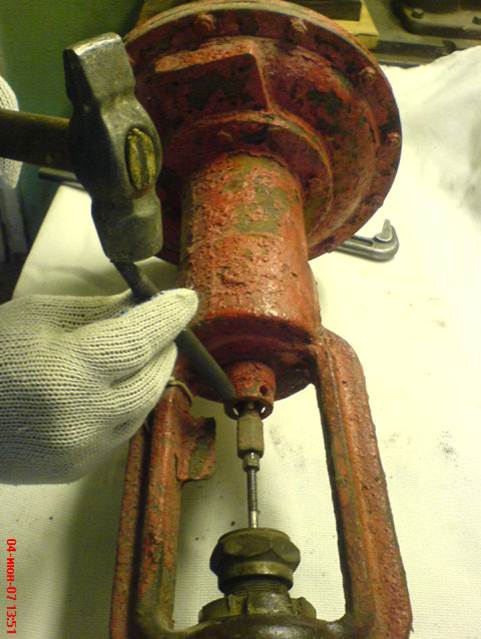
4. При подаче сжатого воздуха в мембранную полость исполнительного механизма шток не перемещается.
Возможные причины |
Способы устранения неполадок |
Повреждение мембраны вследствие превышения давления сжатого воздуха предельного значения или же вследствие попадания на мембрану (вместе с воздухом или иным путем) масла, бензина или других нефтепродуктов, разрушающе действующих на материал мембраны |
Разобрать мембранный исполнительный механизм и заменить дефектную мембрану исправной. При этом толщину и число матерчатых прослоек резины следует подобрать одинаковыми с той, которая удаляется |
5. При регулировании расхода протекающего вещества затвор мембранного исполнительного устройства чаще всего занимает положение, близкое к одному из крайних.
Возможные причины |
Способы устранения неполадок |
Если при нормальной работе регулятора затвор почти закрывает отверстие седла или, наоборот, открывает его почти полностью и при этом давление в мембранной полости близко к предельному, то это указывает на то, что условный диаметр мембранного исполнительного устройства либо велик, либо мал для данного трубопровода и расхода в нем |
В соответствии с действительным расходом протекающего по трубопроводу вещества выбрать соответствующий условный проход мембранного исполнительного устройства и при наличии мембранного исполнительного устройства с таким условным проходом установить его. Если подходящего исполнительного устройства в наличии нет и имеется возможность выточить новый затвор, то рассчитать профиль нового затвора и заменить в мембранном исполнительном устройстве старый затвор на новый |
Исполнительные механизмы
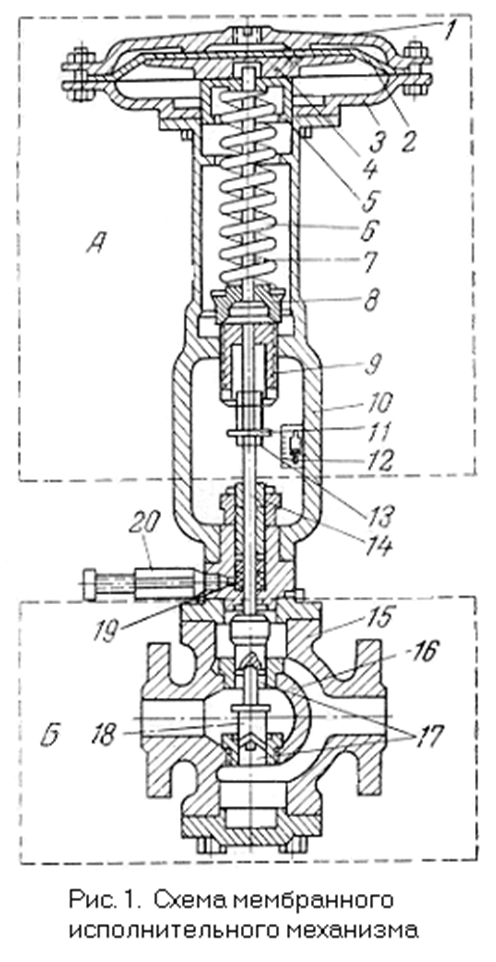
Привод А состоит из:
1 — верхняя крышка, 2 — эластичная мембрана из плотной прорезиненной ткани, 3 — нижняя крышка, 4 — металлический диск, 5 — направляющий стакан, 6 – пружины, 7 – шток, 8 – опора, 9 – гайка, 10 – кронштейн, 11 – диск, 12 – шкала, 13 — соединительной гайкой, 14 – штоком,
Регулирующий орган Б включает в себя:
15 – корпус, 16 – перегородкой, 17 — с цилиндрическими отверстиями, 18 – клапан, 19 – сальник, 20 – лубрикатором
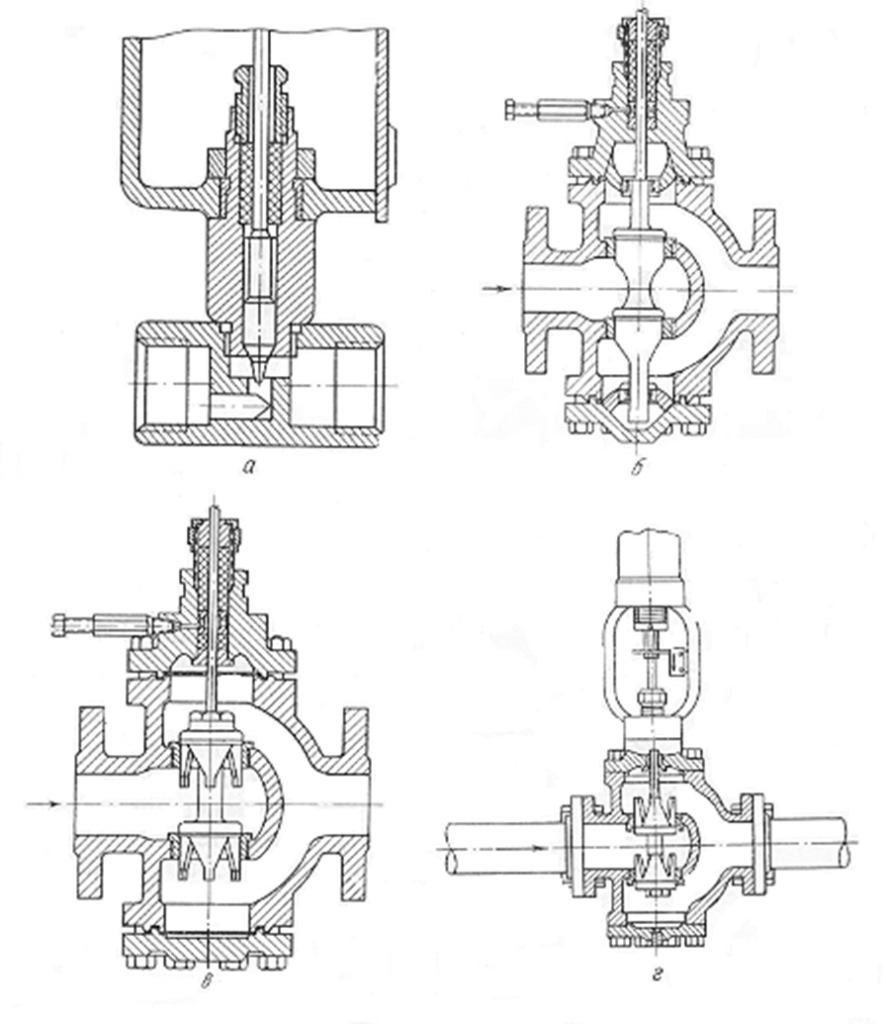
Обычно регулирующие органы исполнительных механизмов, устанавливаемых в трубопроводах больших диаметров, выполняются двухседельными (см. рис.б, в, г) для уменьшения усилий на клапан со стороны среды при больших перепадах давления. Односедельные регулирующие органы применятся для установки в трубопроводах малого диаметра и при небольших перепадах давления на клапане (см. рис. а)
Разборка и сборка регулирующего клапана.
Разборка мембранных исполнительных устройств.
Разборку нормально открытого исполнительного устройства производят для выявления состояния отдельных деталей, чистки и ремонта следующим образом.
Все видимые поверхности исполнительного устройства (корпус, мембранный исполнительный механизм и т. д.) обдувают из шланга сжатым воздухом и тщательно очищают от грязи.
Вращая контргайку 5 (рис. 1), освобождают специальную гайку 2, после чего вращением этой гайки отсоединяют шток плунжера от промежуточного штока. Если исполнительное устройство имеет пневматический позиционер, то освобождают его рычаг для возможности отделения мембранного исполнительного механизма от корпуса регулирующего органа. Отворачивают специальную гайку 11 (рис. 2) и отделяют мембранный исполнительный механизм от корпуса регулирующего органа.
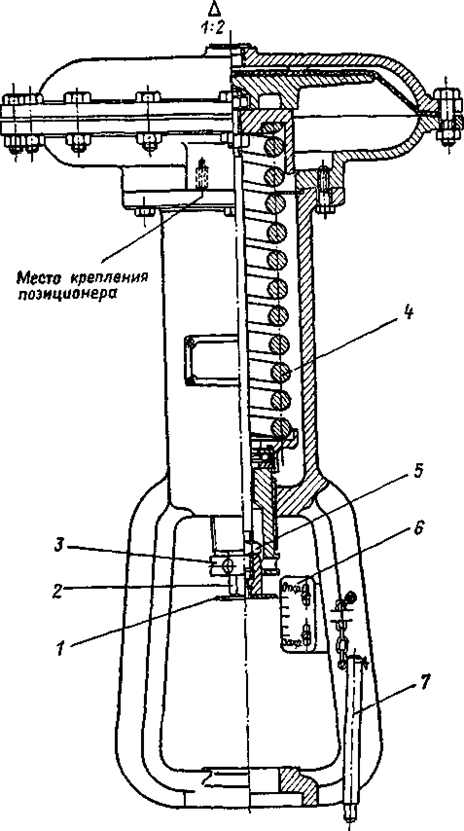
Рисунок 1.
Ремонт мембранных исполнительных устройств.
При этом крупные механизмы поднимают талями или лебедками. Освобождают шток затвора от гаек. Проверяют вручную легкость перемещения затвора до крайних положений.
Разборка исполнительного устройства регулирующего клапана.
Осторожно отвертывают гайки шпилек или болтов на верхней крышке 4 (рис 2), чтобы не перегрузить отдельные крепежные детали и не снизить их надежность. Эту работу производят в два приема: сначала по способу диаметрально противоположного обхода поворачивают все гайки на 1/8 полного их оборота, а затем в любом порядке отворачивают все гайки. Снизив давление масла в сальниковом устройстве, удаляют лубрикатор (масленку). Помечают положение крышки на корпусе для установки ее в дальнейшем на прежнее место. Осторожно, чтобы не повредить шток и затвор, отделяют верхнюю крышку 4 от корпуса 3. Если крышка тяжелая, то подъем ее осуществляют талями или лебедкой. При подъеме следят за строго вертикальными перемещениями крышки.
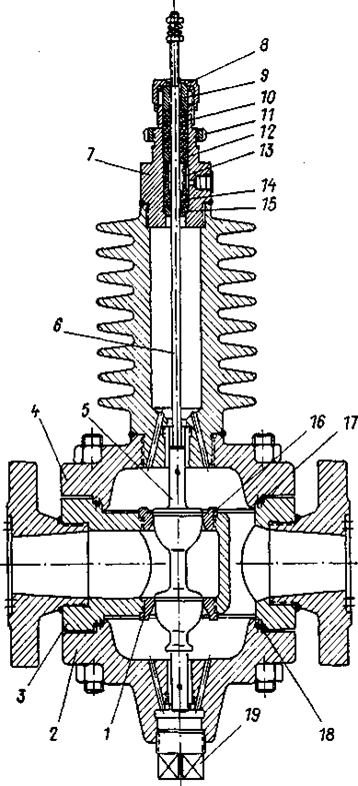
Рисунок 2.
Удаляют затвор 5 со штоком 6 и тщательно очищают их поверхность от грязи и остатков сальниковой набивки. При этом запрещается пользоваться острым металлическим инструментом (зубилом, ножом, шилом и т.п.) во избежание повреждения очищаемых поверхностей. Отворачивают накидную гайку 8 и удаляют грундбуксу 9, кольца 15 и 12, втулку 13 и остатки сальниковой набивки 14 и 10. Сальниковую камеру, грундбуксу, кольца и втулку тщательно очищают от следов набивки, не применяя при этом острых металлических инструментов.
Отмечают положение нижней крышки 2 относительно корпуса. Отворачивают гайки на шпильках или болтах и отделяют нижнюю крышку 2 от корпуса 3 клапана. Отворачивают пробку 19. Производят промывку и чистку корпуса и крышек. Закончив чистку нижней крышки, заворачивают пробку 19. Промывают и очищают от наслоений седла 1 и 16 и при необходимости замены или ремонта выворачивают их из корпуса.
В нормально закрытых исполнительных устройствах снимают сначала нижнюю крышку, а затем через образовавшееся отверстие удаляют затвор со штоком.
При разборке мембранных исполнительных устройств, имеющих конструктивные отличия от описанной конструкции, учитывают болтовое крепление мембранного исполнительного механизма к крышке регулирующего органа, соединение штоков посредством резьбовой втулки со стопорными винтами и крепление штока к затвору посредством разъемной головки.
Сборка исполнительного устройства регулирующего клапана.
Сборку нормально открытого исполнительного устройства с пневматическим позиционером производят следующим образом (обозначения приведены на рис. 2).
1. В корпус 3 регулирующего органа ввертывают седла 1 и 16 до отказа. При этом не допускается применение зубил, наставок и т.п. инструментов и посадка седла в гнезда на сурике или на графите с маслом. Ввертывание седел выполняют специальными ключами или приспособлениями. Седло должно ввинчиваться с усилием, т.е. должна иметь место плотная посадка с незначительным натягом; шатание седла при ввинчивании не допускается. При условном проходе регулирующего органа Dy = 20 мм ввертывание седла производят двое рабочих, используя рычаг длиной 220 мм. При этом они создают крутящий момент 151 Нм (1540 кгс/см2) при усилии на рычаге 700 Н (70 кгс).
При условном проходе регулирующего органа Dy = 50 мм двое рабочих, используя рычаг длиной 1300 мм, при ввертывании седла создают крутящий момент 892 Нм (9100 кгс/см2) при усилии на рычаге 700 Н (70 кгс). При условном проходе Dy = 100 мм для ввертывания седла требуется уже действие четырех рабочих, использующих рычаг длиной 2500 мм и создающих крутящий момент 2432 Нм (35 000 кгс/см2) при усилии на рычаге ключа 1,4 кН (140 кгс).
При ввертывании натуго седло может деформироваться. Отсутствие деформации определяют посредством контрольной плиты. Деформированное седло заменяют. Установка между телом корпуса регулирующего органа и седлом различных прокладок не дает положительных результатов.
2. Под нижнюю крышку 2 устанавливают алюминиевую или стальную прокладку 18 толщиной 2 мм, после чего помещают нижнюю крышку на свое место, совмещая ранее нанесенные при разборке регулирующего органа отметки на крышке и корпусе, и закрепляют крышку гайками на шпильках или болтах. Алюминиевую прокладку ставят, если регулирующий орган не имеет ребристой рубашки, т.е. будет работать при температуре рабочей среды не выше 200 °С, а стальную прокладку ставят, если регулирующий орган имеет ребристую рубашку, т. е. рассчитан для работы при температуре протекающего вещества выше 200 °С, например до 450 °С.
Вместо алюминиевых или стальных прокладок допускается применение паронитовых или клингеритовых прокладок толщиной 2 мм, но они менее надежны по сравнению с алюминиевыми или стальными, вследствие незначительной ширины кольцевой поверхности прокладок. Не допускается применение паронитовых или клингеритовых прокладок со следами излома, морщинами и трещинами. По поверхности и краям допускается незначительная ворсистость.
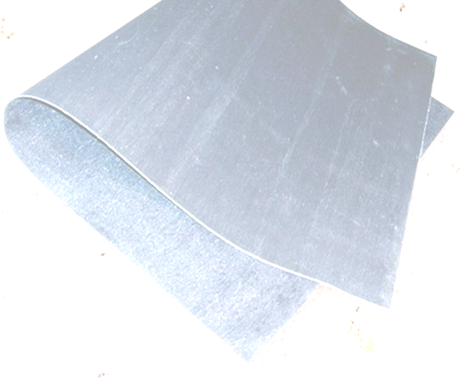
Прокладки при загибе на 180° вокруг стержня с диаметром 42 мм не должны ломаться, трескаться и расслаиваться. Завертывание гаек на шпильках или болтах вначале производят нормальным ключом без рычага, с затягиванием шпилек или болтов в диаметральном положении. После круговой затяжки шпилек или болтов ключом нормальной длины применяют рычаги, соблюдая правило крестообразного обхода гаек. При креплении гаек натуго не допускаются удары кувалдой по ключу. В этом случае применяют удлиненные гаечные ключи или на короткие ключи надевают трубки для удлинения рукоятки. Затягивать гайки на шпильках или болтах диаметром до 16 мм должен один рабочий, применяя рычаг длиной 500 мм, на шпильках или болтах диаметром от 17 до 25 мм — двое рабочих, применяя рычаг длиной 1000 мм, на шпильках или болтах от 26 до 48 мм — трое рабочих, применяя рычаг длиной 1500 мм. Крышка считается закрепленной после трехкратного подтягивания гаек на всех шпильках (болтах) гаечным ключом с рычагом.
3. Установив корпус регулирующего органа с нижней крышкой на тиски, если позволяют размеры корпуса, или при положении указанных деталей на полу помещения, если регулирующий орган велик по габаритам, производят притирку посадочных поверхностей плунжера и седел следующим образом. Посадочные поверхности плунжера и седел промывают бензином и вытирают насухо. Притирку производят, например, смесью наждачного порошка с машинным маслом. Наждачный порошок получают, отобрав магнитом металлическую часть пыли, остающейся при заточке резцов на наждачных кругах. Нанесенный на притираемые поверхности слой должен быть равномерным и не слишком густым. После шестисемикратного поворота плунжера рукой по дуге вправо и влево на 1/4 окружности плунжер слегка приподнимают и, повернув на 180° по часовой стрелке, вновь опускают на седло и повторяют операцию притирания.
Перекладывание плунжера повторяют пять раз, после чего притираемые поверхности промывают бензином и вытирают насухо. Повторяют притирку, применяя микропорошки (от М-28 до М-7), после чего производят доводку пастой ГОИ (Государственного оптического института имени С. И. Вавилова). Паста ГОИ выпускается для грубой доводки — черного цвета, для средней — темно-зеленого и тонкой — светло-зеленого. Перед нанесением пасты притираемые поверхности смачивают керосином. При окончательной доводке слой пасты, наносимый на поверхности седел и затвора, должен быть минимальным. При хорошей притирке поверхности должны быть совершенно одинаковые «на отблеск», без бликов, штрихов и т. п. Затвор при подъеме должен присасываться к седлам в корпусе. Задачей притирки является обеспечение плотной и одновременной посадки затвора на седла в корпусе. Весь процесс притирки затвора и седел ведут, стараясь не создавать добавочного давления затвора на седла, кроме массы самого затвора.
4. Ввертывают шток 6 в затвор 5 (рис. 2) и стопорят его штифтом, после чего затвор со штоком устанавливают на место, т. е. на седла. Со штока удаляют крепежные гайки (рис.3).
5. Устанавливают верхнюю алюминиевую или стальную прокладку 17 толщиной 2 мм, после чего осторожно помещают верхнюю крышку 4 на свое место, совмещая отметки на крышке и корпусе, сделанные ранее при разборке регулирующего органа, и закрепляют крышку гайками на шпильках или болтах. Затяжку гаек выполняют методом, указанным при описании установки нижней крышки.
6. Устанавливают нижнее сменное металлическое кольцо сальника 15, затем кольца сальниковой набивки 14 и втулку сальника («фонарь») 13. Подачу сальниковых колец внутрь втулки 7 крышки производят отрезком трубки, имеющей внутренний диаметр, достаточный для того, чтобы ее можно было насадить на шток затвора. Над нижним сменным кольцом 15 толщина сальниковой набивки 14 должна быть такой, чтобы нижние отверстия втулки 13 располагались против отверстия для лубрикатора (масленки). Устанавливают лубрикатор и заполняют его и втулку 13 смазкой.
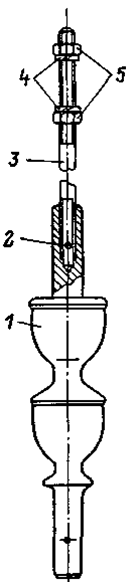
Рисунок 3.
Смазка к стальным клапанам — оссоголин марки 300-AAA; к чугунным клапанам – смазка марки НК-50. Затем устанавливают верхнее сменное металлическое кольцо 12, несколько колец сальниковой набивки 10, грундбуксу 9. Толщина сальниковой набивки над верхним сменным кольцом 12 должна быть такой, чтобы грундбукса 9 после ее установки выступала из втулки 7 верхней крышки на 80 % своей высоты.
Этим достигается возможность перемещения грундбуксы вниз при затяжке сальника. Для стальных регулирующих органов используют сальниковые кольца из прессованного асбеста, а для чугунных — асбестовый шнур, пропитанный специальным составом. В последнем случае берут асбестовый шнур и варят его в таком составе: 18% графита, 11% резинового клея, 5% тавота 66 % вазелина. Для приготовления резинового клея 200 г невулканизированной резины растворяют при нагревании в 250 г вазелинового масла. Состав приготовляют следующим образом: вазелин и тавот расплавляют на водяной бане, после чего раствор снимают с бани и в него при энергичном перемешивании вливают резиновый клей, а затем также при энергичном перемешивании порциями всыпают графит до загустения, в результате чего раствор считают готовым.
Приготовление колец из шнура производят, навивая шнур на стержень, имеющий одинаковый диаметр со штоком, и разрезая шнур под углом (косая разрезка), как показано на рис. 4. Заготовленные кольца опрессовывают каждое в отдельности в приспособлении, представляющем собой по размерам копию сальникового устройства регулирующего органа, после чего хранят в закрытых коробках во избежание загрязнения. При укладке в сальник соединение кольца выполняют внахлестку, срезами под 45°. Стыки отдельных колец при этом смещают относительно друг друга на 90° согластно ГОСТ 5152-84. Надевают накидную гайку 8 и, вращая ее рукой без помощи ключа, затягивают сальник. Затяжку сальника считают нормальной, когда шток, будучи предварительно поднятым рукой, а затем отпущенным, плавно опускается под действием собственного веса. С повышением давления возникает необходимость в более значительной затяжке сальника. Нужная герметичность сальника достигается увеличением давления смазки от лубрикатора. Устанавливают мембранный исполнительный механизм на регулирующий орган и закрепляют его специальной гайкой 11 (рис. 2).
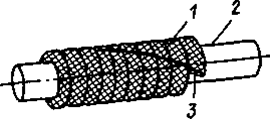
Рисунок 4. Приготовление колец сальниковой набивки
1 — сальниковый шнур; 2 — стержень; 3 — линия разреза.
9. Навинчивают гайку на шток, после чего второй гайкой ее стопорят. Надевают рычаг от позиционера на шток, затем указатель 1 (рис. 1), после чего навинчивают на шток специальную гайку 2, которой соединяют шток затвора с промежуточным штоком. Посредством гайки 5 фиксируют положение гайки 2. Если при этом указатель/окажется смещенным относительно шкалы 6 положения затвора, то перемещают последнюю так, чтобы против указателя оказалась надпись «Открыто».
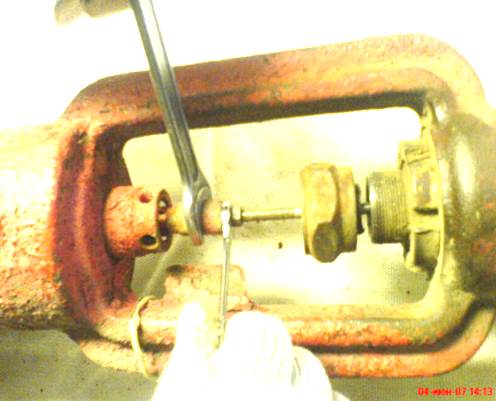
Закрепляют позиционер на корпусе мембранного исполнительного механизма и соединяют рычаг с тягой, после чего собранное исполнительное устройство поступает на регулировку.
Сборка нормально закрытого исполнительного устройства отличается от описанной сборки тем, что соответственно меняют положение седел и затвора и после установки верхней крышки, не устанавливая нижнюю крышку, производят притирку затвора и седел. В дальнейшем изменяют положение шкалы поворотом на 180°.
При регулировке в мембранную полость подают давление сжатого воздуха и, изменяя натяжение пружины 4, добиваются полного хода затвора при изменении давления от минимального до максимального значения. Регулировку ведут ключом 7, вращая резьбовую втулку 3. При давлении, равном 50 % максимального давления в мембранной полости исполнительного устройства, верхний рычаг позиционера должен быть параллелен рычагу, закрепленному на штоке затвора. В противном случае регулируют длину вертикальной тяги, прикрепленной нижним концом к указанному рычагу и передающей его движение к механизму позиционера.
Сборку мембранных исполнительных устройств иной конструкции производят в такой же последовательности, как указано выше, но при этом учитывают конструктивные особенности этих исполнительных устройств, а именно: болтовое крепление мембранного исполнительного механизма к верхней крышке регулирующего органа, соединение штоков посредством резьбовой втулки со стопорными винтами и крепление штока к затвору посредством разъемной головки, другую конструкцию связи позиционера со штоком затвора. При сборке устанавливают паронитовые прокладки толщиной 2 мм под верхнюю и нижнюю крышки корпуса регулирующего органа и толщиной 1 мм под колпачок головки затвора. При отсутствии указателей положения затвора укрепляют на кронштейне посредством хомутика шкальную пластинку, под резьбовую втулку помещают указатель.
Переделка нормально открытого исполнительного устройства в нормально закрытое.
Нормально открытое исполнительное устройство отличается от нормально закрытого только расположением седел, затвора и шкальной пластинки. На рис. 2 представлено нормально открытое исполнительное устройство. Для переделки этого устройства в нормально закрытое, руководствуясь изложенной методикой разборки и сборки этих устройств, отделяют верхнюю 4 и нижнюю 2 крышки; сняв шпильку, вывинчивают шток 6 из затвора 5 и затем, завинтив шток 6 в противоположный конец затвора 5, фиксируют это положение шпилькой; вывинчивают седла I и 16 и меняют их местами, т. е. седло 1 ввинчивают на место седла 16 и, наоборот, седло 16 ввинчивают на место, занимаемое ранее седлом 1; устанавливают затвор, пропуская шток снизу через отверстия седел; собирают исполнительное устройство; шкальную пластинку устанавливают так, чтобы вверху ее была надпись «Закрыто», а в нижней части — надпись «Открыто».
Переделка нормально закрытого исполнительного устройства в нормально открытое сводится к тем же операциям, но шкальную пластинку устанавливают в положение, при котором в верхней ее части находится надпись «Открыто», а в нижней — надпись «Закрыто».
Переделка исполнительных устройств некоторых конструкций из нормально закрытых в нормально открытые или наоборот, вследствие неприспособленности затвора для этой цели, производится при наличии запасного затвора, имеющего соответственно расположенную присоединительную мембранную полость (рис. 5).
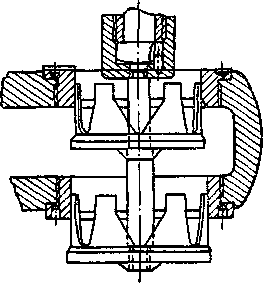
Рисунок 5. Полый затвор двухседельного регулирующего органа нормально закрытого исполнительного устройства
Ремонт корпусов и крышек исполнительных устройств.
Для выявления необходимости ремонта корпусов и крышек исполнительных устройств вначале их тщательно осматривают, особенно в участках резкого перехода сечений, около ребер и перехода корпуса к фланцу, а затем производят гидравлическое испытание корпуса и крышек на прочность.
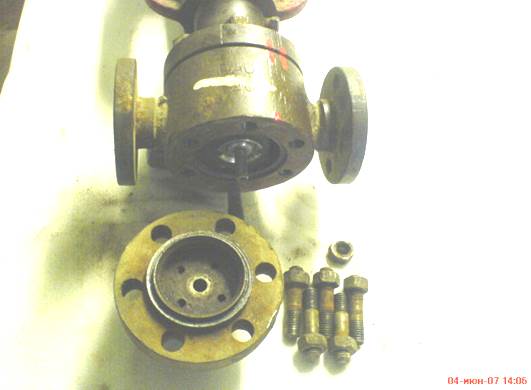
Испытание на прочность производят гидравлическим прессом при испытательном давлении Ри = 2,4 МПа (24 кгс/см2) для испольнительных устройств с Ру = 1,6 МПа (16 кгс/см2), Ри = 6 МПа (60 кгс/см2) для исполнительных устройств с Ру = 4 МПа (40 кгс/см2) и при испытательном давлении Ри = 9,6 МПа (96 кгс/см2) для исполнительных устройств с Ру = 6,4 МПа (64 кгс/см2). При испытании пресс целесообразно заполнять керосином или маслом, так как водяное заполнение пресса приводит к появлению ржавчины в дефектных местах. Выявленные трещины, сквозные и глубокие раковины в корпусах и крышках исправляются электродуговой сваркой. Места под сварку разделывают пневматическим или ручным режущим инструментом (зубилом, напильником, сверлом и т. п.). Выплавка дефектного места автогеном не рекомендуется во избежание ослабления прочности металла вследствие выгорания углерода при выплавке.
При ремонте чугунных корпусов и крышек применяют холодную сварку электродами марки ОЗЧ-4. Толщина покрытия должна быть 1,0 — 1,2 мм при диаметре стержня 3 мм, т. е. после покрытия диаметр электрода будет 5,0 — 5,4 мм; 1,25 — 1,40 мм — при диаметре стержня 4 мм и 1,5 — 1,7 мм — при диаметре стержня 5 мм. Отношение массы покрытия к массе стержня для электродов всех диаметров составляет примерно 35%.
Чугун, наплавленный таким электродом, поддается механической обработке твердосплавным режущим инструментом. Сварку производят участками. Каждый участок для снятия напряжений и уплотнения металла шва подвергают непосредственно после сварки ковке молотком вручную. Швы выполняют не менее чем в два прохода. Заварку трещин ведут обратноступенчатым способом.
Сварку осуществляют на постоянном токе при обратной полярности. Сварочный ток составляет примерно 25 — 30 A на 1 мм диаметра электрода. Сварку ведут короткими швами (примерно 30 мм) с охлаждением на воздухе до 60°С.
При ремонте корпусов определяют состояние резьбы в корпусе для ввертывания седел: проверяют чистоту обработки и плотность посадки седла. Резьба не должна иметь заусениц, выкрошенных ниток, вмятин и др., а также следов износа рабочим веществом. Резьба должна быть чистой, шлифованной и соответствовать 2-му классу точности. Плотность посадки резьбы проверяют при отвинчивании и завинчивании седел, которые должны отвинчиваться или завинчиваться с некоторым усилием (плотная посадка).
При ремонте корпусов определяют состояние резьбы под шпильки. Если резьба изношена и толщина стенки между шпильками достаточна, то нарезают новую резьбу несколько большего размера и изготовляют под этот размер шпильку. Если толщина стенки мала, то в отверстие под шпильку впрессовывают цилиндрик и, заварив его с двух сторон, высверливают в нем отверстие и нарезают резьбу под шпильку.
Вывертывание дефектных шпилек иногда представляет трудности, особенно это относится к шпилькам, часть которых отломана. В последнем случае в шпильке просверливают отверстие на глубину 10 — 15 мм и делают его квадратным, после чего вставляют квадратный стержень и ключом вывертывают шпильку из корпуса. Иногда приваривают к шпильке стержень и затем вывертывают ее.
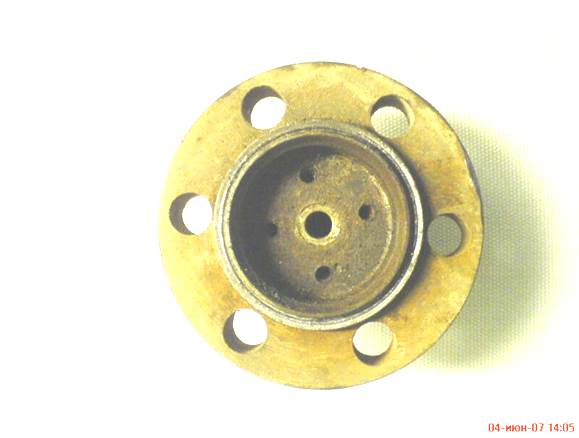
Ремонт седел и затворов.
На износ рабочих поверхностей седел и затвора оказывают влияние два фактора: коррозия и эрозия.
Коррозия проявляется в разрушении поверхностей указанных деталей под действием протекающего вещества, химически взаимодействующего с материалами, из которых детали изготовлены. Степень разрушения можно уменьшить соответствующим подбором материалов, идущих на изготовление седел и затвора.
Эрозия проявляется в разрушении поверхностей седел и затвора вследствие истирающего воздействия рабочего вещества. Эрозия особенно проявляется в условиях, когда клапан открыт еще мало, так как при этом образуется узкий кольцевой проход между седлами и затвором и истирающее воздействие рабочего вещества возрастает. Эрозионный износ возникает и при неправильном выборе материала для изготовления седел и затвора или несоблюдении режимов их термической обработки.
В результате процессов коррозии и эрозии изменяется конфигурация седел и затвора исполнительного устройства, что нарушает характеристику последнего. Кроме того, появляется недопустимый пропуск протекающего вещества при полностью закрытом исполнительном устройстве. Односторонние разрушения рабочей поверхности седел приводят к искривлению штока и возрастанию трения затвора в опорных направляющих втулках, что вначале вызывает увеличение зоны нечувствительности, а затем — полное прекращение перемещений затвора.
Для восстановления изношенных уплотнительных поверхностей седел и затвора применяют наплавку легированными электродами, что сокращает расход дефицитных легированных сталей. Наплавку седел и затворов клапанов, работающих при высокой температуре протекающего вещества, целесообразно производить электродами, предназначенными для дуговой сварки высоколегированными сталями с особыми свойствами. Покрытие должно быть толстое или особо толстое.
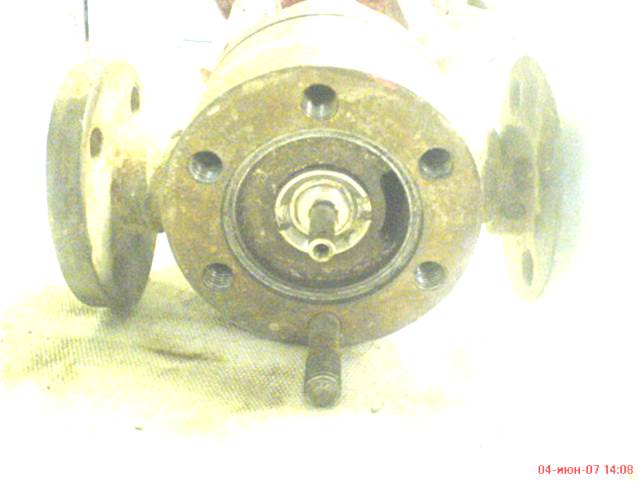
Выпуск из ремонта исполнительных устройств.
Внешний осмотр перед испытаниями.
Цель: установить пригодность отремонтированного исполнительного устройства к дальнейшим испытаниям для выпуска из ремонта.
Требования: цвет окраски корпуса регулирующего органа и исполнительного механизма должен соответствовать применяемым для изготовления этих деталей материалам (корпуса из углеродистых сталей — серый цвет, из легированных кислотостойких и нержавеющих сталей — голубой цвет, из чугуна — черный цвет; мембранные исполнительные механизмы — оранжевый или черный цвет и т. п.); окраска корпуса регулирующего органа и исполнительного механизма не должна иметь дефектов, ухудшающих внешний вид клапана; у всех деталей, имеющих резьбу, последняя не должна иметь дефектных ниток, должна быть чистой, без заусениц; все винты, болты, гайки, шпильки и другие детали, входящие в комплект регулирующего органа, должны иметься в наличии.
Испытание регулирующих органов на герметичность в седлах и прокладках.
Испытание регулирующих органов на герметичность в седлах и прокладках производят гидравлическими прессами, заполненными керосином или маслом, имеющим вязкость не более 2° Е. При испытании регулирующего органа на герметичность в прокладках и сальнике керосин или масло подводят через отверстие выходного фланца, а отверстие входного фланца закрывают. Испытание ведут под давлением, равным условному давлению.
При испытании регулирующего органа на герметичность затвора в седлах керосин или масло подводят через отверстие входного фланца, а отверстие выходного фланца закрывают. В этом случае испытательное давление для всех типов регулирующих органов должно составлять 1 МПа (10 кгс/см2). С поверхности первого наплавленного валика молотком сбивают шлак и зачищают металлической щеткой, как сам валик, так и наплавляемую поверхность седла или затвора, прилегающую к валику. Недостаточно полное удаление шлака, брызг металла и т. п. затруднит Наложение второго валика и приведет к пористой и неровной его наплавке.
Повторяя операции пп. 3 и 4, наплавляют второй валик (второй слой). Общая высота наплавки составит 4 — 6 мм. Наплавку опять ведут в том же направлении, при этом начало шва перекрывают на длине 10 — 15 мм. Наплавку продолжают до получения нужной величины наплавленного слоя с припуском на механическую обработку не менее 3 мм на каждую сторону и 3 — 5 мм по высоте. На поверхности наплавленного слоя допускается некоторое количество мелких пор и раковин диаметром не более 1 мм при условии, что они будут удалены при последующей механической обработке.
Наплавленное седло или затвор подвергают термической обработке — отпуску при температуре’ 500 — 550°С с выдержкой при этой температуре в течение 2 ч с последующим медленным остыванием (вместе с нагревательной печью).
Наплавленный сплошной затвор устанавливают на токарный станок и обрабатывают под шаблон, вначале снимая лишний металл резцом, затем — личным бархатным напильником, тонкой стеклянной бумагой, и полируют полировочной пастой.
Окончательную расточку наплавленных седел производят совместно с корпусом на токарном станке. Для этого седла завинчивают в корпус клапана с захлесткой в резьбе и до получения герметичности плоских уплотнительных поверхностей (возле резьбы).
При изготовлении нового седла или обработке наплав» ленного седла на токарном станке допускается эксцентриситет пропускного (посадочного) отверстия и резьбовой окружности седла не более 0,02 мм на 100 мм длины диаметра.
Для выверки конфигурации седел нужны два шаблона — шаблон профиля верхнего седла и шаблон профиля нижнего седла. Изготовление этих шаблонов не представляет сложности, так как по существу у седла важно лишь выдержать профиль посадочной поверхности, ее месторасположение и диаметр прохода. Вид профиля входной части седла особого значения не имеет. При испытании нормально открытых исполнительных устройств для их закрытия в мембранную полость подается воздух под предельным давлением срабатывания, а нормально закрытые исполнительные устройства должны закрываться нормальным установочным натяжением пружины.
Регулирующие исполнительные устройства, предназначенные для работы в газовых средах (пар, воздух, газы), подвергают дополнительному испытанию на герметичность в сальнике и прокладках давлением воздуха, подаваемого со стороны выходного фланца, 1,3 МПа (13 кгс/см2) — для чугунных регулирующих органов, 2,2 МПа (22 кгс/см2) — для стальных регулирующих органов на Ру = 4,0 МПа (40 кгс/см2) и 3,4 МПа (34 кгс/см2) — для стальных регулирующих органов на Ру = 6,4 МПа (64 кгс/см2).
Требования:
пропуск керосина или масла через уплотнительные прокладки или сальник при испытании герметичности не допускается;
количество керосина или масла, прошедшее в минуту через уплотнительные поверхности седел, в зависимости от условного диаметра регулирующего органа не должно превышать следующих значений:
Диаметр регулирующего органа Dy, мм |
15 — 25
|
50 — 80 |
100 — 125 |
150 |
200 |
250 — 300
|
Количество керосина или масла, см3 |
10
|
20 |
30 |
40 |
50 |
75
|
Утечка воздуха через прокладки и сальниковую набивку при испытании давлением воздуха не допускается.
Проверка качества сборки исполнительного устройства.
Проверку качества сборки исполнительного устройства выполняют на установке, представленной на рис. 6.
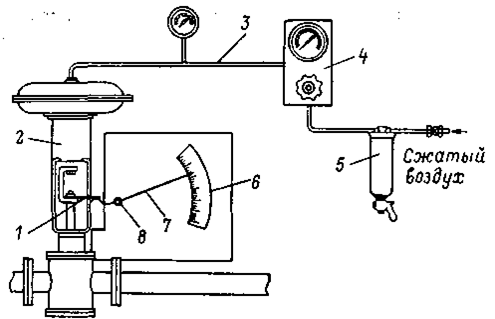
Рисунок 6.
К штоку испытуемого исполнительного устройства 2 прикрепляют пластинку /, которая при перемещении затвора воздействует на изогнутый конец стрелки 7, имеющей осевое крепление в точке 8. Ось 8 стрелки укрепляется на неподвижной доске, временно прикрепленной к верхней крышке корпуса исполнительного устройства. Отношение длины плеч стрелки берут примерно 15:1 в целях увеличения длины шкалы 6. Шкалу предварительно градуируют в процентах хода штока исполнительного устройства, т. е. размечают на сто равных частей.
В мембранную полость через фильтр 5 и панель дистанционного управления 4 по трубке 3 подают сжатый воздух, давление которого измеряют образцовым манометром (давление сжатого воздуха перед редуктором должно составлять 150 — 200 кПа). Изменяя натяжение регулировочной пружины, добиваются полного хода затвора при изменении давления воздуха в мембранной полости в рабочих пределах.